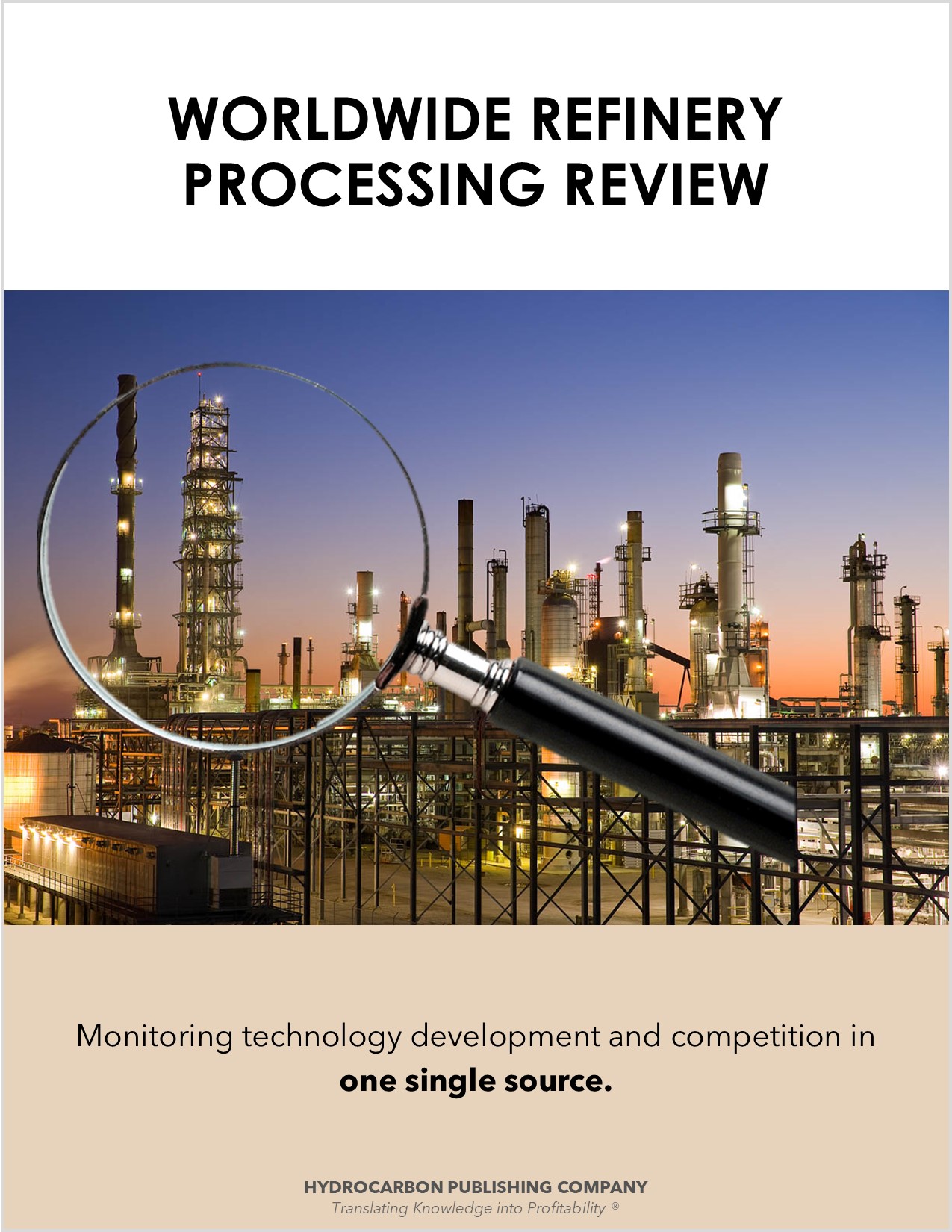
Globally, octane requirement is a dominant issue in major gasoline-consuming countries (such as the US, Japan, and China). Europe is diesel-centric and higher octane specification can be met by blending of MTBE, reformate, and to lesser extent ethanol.
In the US, the need for higher-octane blending components in the gasoline pool is growing as more manufactures are designing their new cars with higher compression engines in order to meet the 2025 Corporate Average Fuel Economy (CAFE) regulations. This is in spite of recent announcements by the Trump administration to place the higher fuel efficiency requirement on hold. Another contributing factor to rising octane demand in the US is the potential for significant octane loss as refiners attempt to comply with tighter standards such as the Tier 3 vehicle and fuel requirements that went into effect in the US in Jan. of 2017. Also exports of gasoline in the US more than doubled from 2010 to 2016 and the RON of most of these export grades ranged from 91 to 95.
One option to recover octane loss is isoparaffin alkylation, which comprises the reaction of isobutane with C3-C5 olefins in the presence of an acid catalyst to produce a high-quality gasoline blendstock product. The product known as alkylate is made up of a mixture of isoheptanes and isooctanes with high octane, low sulfur, and low vapor pressure.
The ongoing shale boom in the US has also created opportunities for operators of alkylation units as the shale boom is providing abundant stocks of cheap butane. Furthermore, the paraffinic nature of tight oils is resulting in a FCC gasoline product that is seeing on average an 8-10 point reduction in octane value meaning refiners will need to account for that octane loss with a high-octane gasoline blending pool component like alkylate.
China has already experienced a significant boost in alkylate demand as evidenced by the construction of several new alkylation plants in the last five years. This country has traditionally relied on the FCC unit for gasoline and diesel production. However, the octane of the gasoline that is obtained is below regulatory standards. Another impetus for increased use of alkylation technology in China is the increased availability of isobutane feedstock obtained from the isomerization of butane in imported liquefied natural gas. The country is also looking into ethanol blending to meet the octane requirement via imports particularly from the US. However, a recent trade spat between China and the US in early 2018 could limit the import of US ethanol due to a potentially higher tariff. MTBE is not a viable option to satisfy the octane requirement in the future as China is banning MTBE sale though conversion of MTBE units to ETBE units is acceptable.
Olefin oligomerization provides another option for the production of gasoline blending components particularly when isobutane is unavailable. The feedstock for this process is primarily propylene and/or butene and the reaction occurs between one olefin and one or more other olefins of the same or different type to produce dimers, trimers and other oligomers. Oligomerization is not utilized as often as in the past and most refineries instead choose alkylation as a more cost-effective process. However, selective dimerization of isobutene can yield high-octane isooctane and can be used to revamp existing facilities used to produce MTBE thereby replacing this gasoline additive with isooctane. The alkylation and olefin oligomerization section also features the latest trends and technology offerings, including:
- Updated look at global gasoline supply and demand including the uptick in demand for high-octane alkylate due to more-stringent gasoline standards and increased processing of paraffinic tight oils;
- Hy-Up distributor tray for Axens Alkyfining alkylation feed pretreatment process;
- CDAlky low-temperature, sulfuric acid alkylation technology from CB&I;
- CDAlkyPlus process from CB&I which combines low-temperature alkylation of isobutylene and isobutane feedstock with olefin pretreatment;
- XP2 Technology from DuPont Clean Technologies that combines two patented sulfuric acid alkylation reactor improvements;
- DuPont Clean Technologies ConvEx technology that allows for the conversion of existing HF alkylation units to H2SO4 units;
- M2Alk three-step solid acid alkylation process from Exelus that uses butanes and methanol as feedstock;
- ISOALKY ionic liquid alkylation process from Honeywell UOP that converts FCC olefins to high-octane alkylate;
- Dimersol-G liquid-phase process from Axens for the dimerization of the propylene product from FCCUs or steam crackers;
- Methods to boost sulfuric acid alkylation unit capacity and throughput; and
- A discussion of the latest patent applications and research papers regarding alkylation technology, including alkylation feedstock preparation; HF alkylation; H2SO4 alkylation; solid acid alkylation; ionic liquid alkylation; and more.