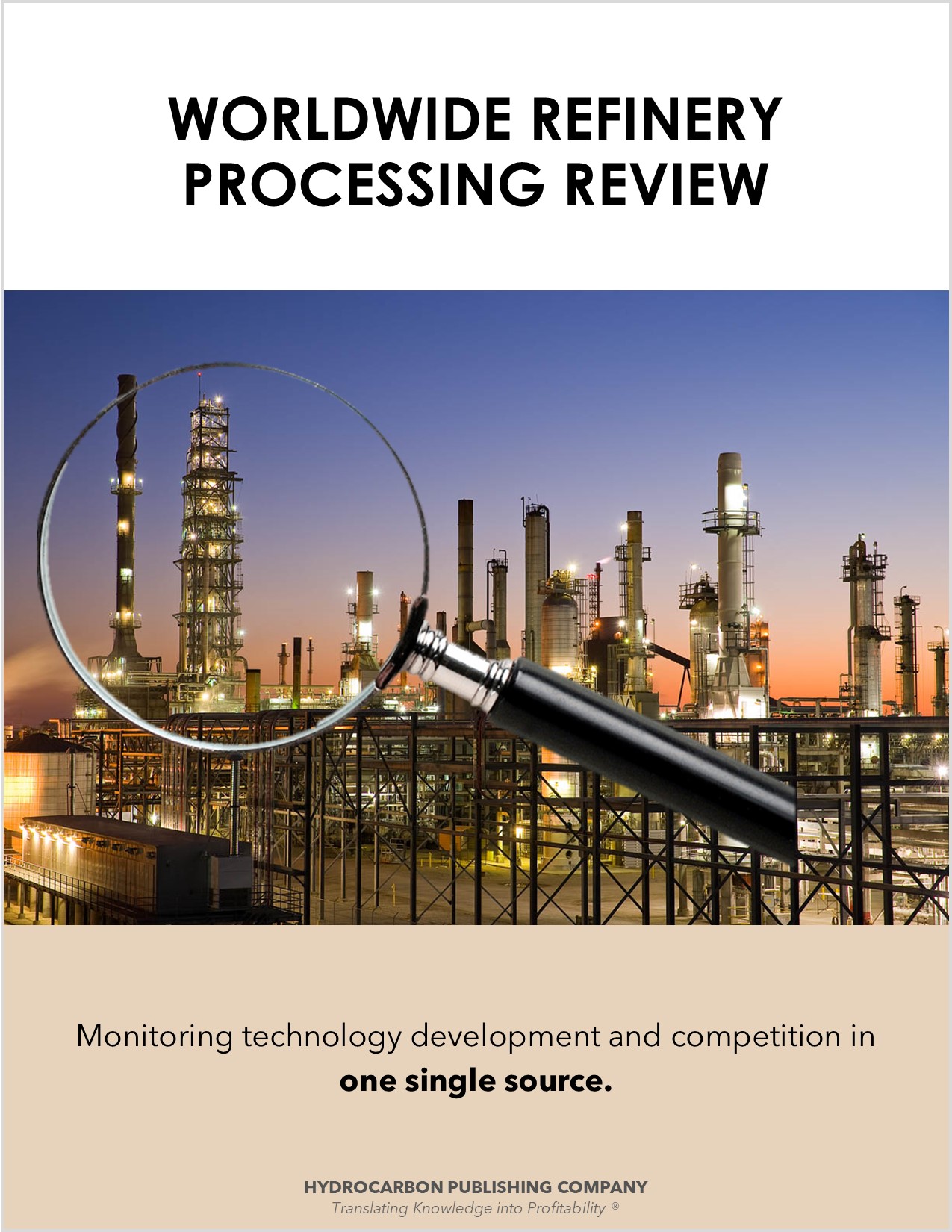
The global refining industry is challenged with maintaining profitability in the face of oil market volatility, shifting refined product specifications and demand, evolving regulatory compliance requirements (e.g. compliance with the IMO's 0.5%-sulfur bunker requirement effective on Jan. 1, 2020), and the coronavirus (COVID-19) pandemic since late 2019 that has devastated transportation fuels demand worldwide as shelter-in-place orders were issued in many parts of the globe. Refining margins have suffered, with many refineries around the world either turning down their operations or completely closing units. At the same time, the pressure is mounting on the refining industry to achieve faster and deeper CO2 emission reductions.
Energy management plays a synergistic role of the refinery operation that connects refining margins, asset management, and environmental regulation compliance. Refinery energy use comprises a significant share of the operating budget, and aside from feedstock costs, is likely the second largest expense on a day-to-day basis. As a result, even small gains in energy efficiency can become profitable, with the added benefit of improving the environmental performance (i.e., lowering the carbon footprint). Because of its high throughput volumes and large energy consumption, the crude distillation unit is the ideal place to focus an energy management program in a refinery setting. Refiners can also examine the other energy-intensive processes used in their facilities in order to maximize their energy efficiencies and reduce CO2 emissions.
Refinery process innovations have been introduced that offer energy consumption benefits. Also available are improved designs and maintenance technologies for heat exchanger networks that can boost savings for a refinery by reducing the fuel burned for heat and lower CO2 emission issues that occur as a result of fuel-burning. The high amount of energy consumed by furnaces is also prompting companies to explore the use of new furnace refractory linings options. Furthermore, refiners have been building cogeneration, combined heat and power, or integrated gasification combined cycle units to save energy and reduce CO2 reduction. Membranes are being explored as an alternative to conventional distillation technology, which can prove quite beneficial in terms of energy and carbon savings. And, with the global push for decarbonization by 2050, green hydrogen produced through electrolysis is garnering increasing interest. Finally, advanced digitalization and the Industrial Internet of Things (IIoT) have become indispensable tools for refiners to improve energy efficiency in various stages of production and for reducing their carbon footprint and sustaining profits in the future.
Additionally, the energy management in decarbonization section features the latest trends and technology offerings, including:
- A new crude distillation process that utilizes an integrated flash drum from CSIR-Indian Institute of Petroleum;
- The IsoTherming process from DuPont Clean Technologies that utilizes a liquid recycle stream instead of a gas recycle;
- Shell Catalysts & Technologies Dual-service Hydrocracking technology with its single main fractionator instead of a stripper-fractionator configurations
- The use of prereforming technology for hydrogen production to improve heat utilization;
- Air Liquide's SMR-X technology that employs a new furnace design with an internal heat exchange system;
- The Haldor Topsøe Convection Reformer (HTCR) and Haldor Topsøe Exchange Reformer (HTER) for hydrogen plants;
- ThyssenKrupp’s convective reformer that can be installed in parallel to a conventional SMR;
- Zhenhai Petrochemical Jianan Engineering’s high-efficiency spiral exchangers;
- Alfa Laval’s Compabloc+ and Packinox heat exchangers;
- The KURITA CD-9931 heat exchanger cleaning agent;
- The Plantweb Insight Heat Exchanger from Emerson for shell-and tube exchanger monitoring;
- KBC's HX (Heat Exchange) Monitor;
- Kurita's HydroBio Advance online monitoring system;
- Analytics tools offered by Seeq Corp.;
- CrudePLUS from SUEZ-Water Technologies & Solutions to address heat exchanger fouling;
- Koch Heat Transfer's Twisted Tube Heat Exchanger Technology;
- Self-cleaning heat exchangers from Klaren Int. and Bronswerk Klarex Technology;
- New furnace refractory linings options from Morgan Advanced Materials;
- EngCHP software from Engineers India Ltd. to optimize the combined heat and power system; and
- A discussion of the latest patent applications related to refinery energy management were issued from 2015 to 2020. Of this total, 99 pertain to innovations that provide energy savings in the major refinery processes of crude distillation (CD), catalytic reforming (CR), hydrotreating (HT), hydrocracking (HC), alkylation, the H2 plant processes, the sulfur plant processes, and coking. Advancements in alkylation and coking account for 26 and 24 patents respectively followed by 14 patents describing hydrogen production and recovery plants, reactors, devices, and processes. Heat exchangers (HX) are the focus of 14 patents as are antifouling additives and fouling reduction methods. And ten patents offer technology solutions specifically designed for waste heat recovery (WHR) from various locations in a refinery.