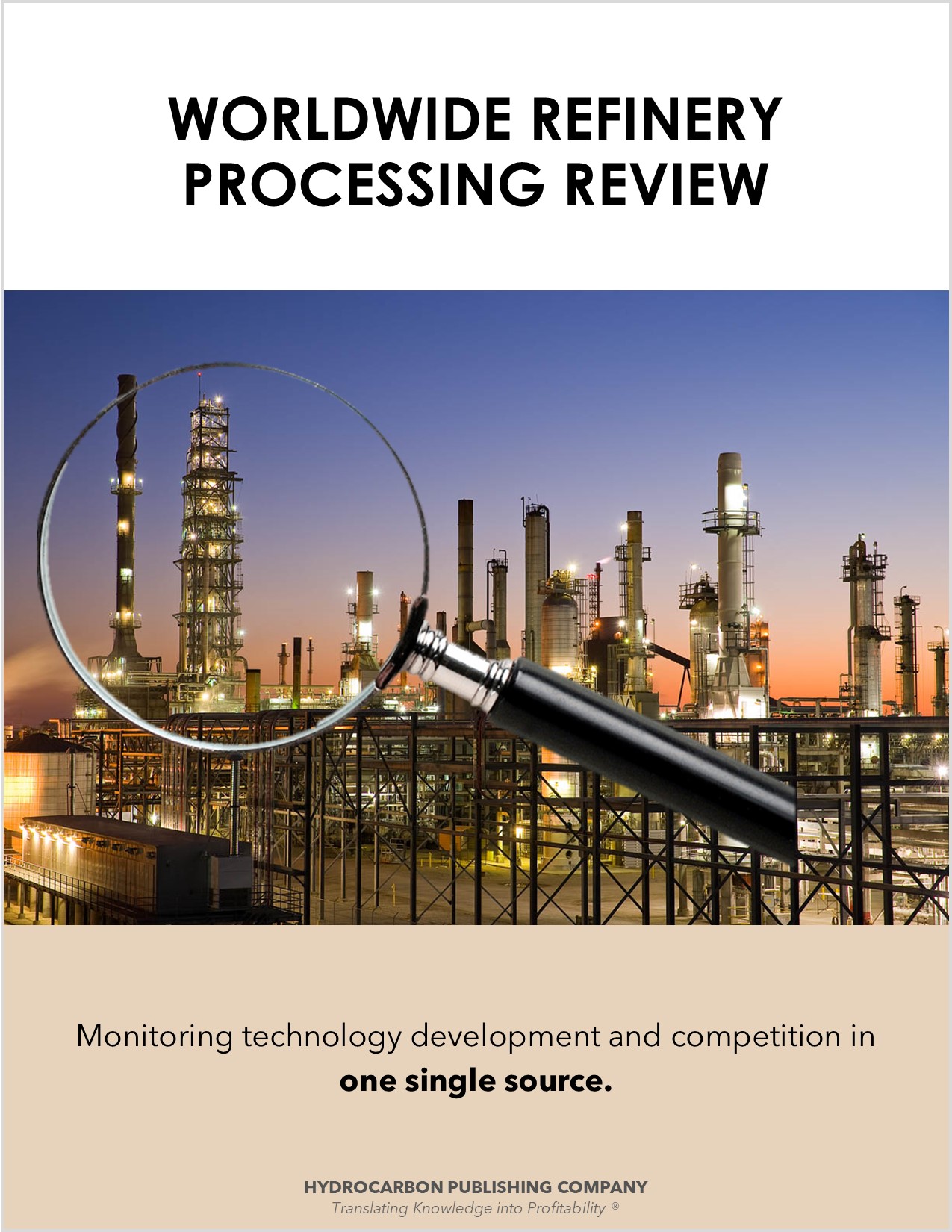
There are several major drivers behind revamp projects undertaken by refiners: retrofitting to accommodate changing crudes (particularly increasing availability of price-advantaged crudes) and making products in demand, meeting environmental and safety regulations, improving profit margins via higher energy efficiency, and marrying the latest information (IT) technologies (e.g. sensors, actuators, wireless devices and so on) and operational technologies (OT) in terms of digital transformation to enhance operational efficiency and further optimize unit performance.
Moving forward, the implementation of advanced technologies (e.g., artificial intelligence) during refinery revamps and turnarounds will become increasingly important to ensure the long-term viability of said refinery. According to vice president and chief technology officer (CTO) for Honeywell Process Solutions Bruce Calder, connectivity will be the main driver for improving a processing plant's productivity, profitability, and safety record. Mr. Calder cites the implementation of the Internet of Things (IoT), which enables physical objects to "both communicate with and sense the world around them" while also providing key information to personnel wherever and whenever it is needed. He says the use of IoT will provide numerous benefits to processing plants including a reduction in unplanned shutdowns, as the availability of timely and meaningful information will allow a problem to be identified before a problem arises. Mr. Calder cites the use of sensors embedded in pipes combined with real-time data from other networked units that can identify hidden corrosion before it leads to a failure. Reducing the number of unplanned shutdowns will not only lead to an increase in plant productivity and profitability but also improve plant safety as well. The use of the cloud within the IoT will be key as data will need to be integrated across a number of processing plants to track information. By having access to these data, businesses can have a better understanding of how plants are performing before large investment decisions are made.
According to Gartner, "Innovations such as smart, connected products, the industrial Internet of Things (IoT), digital twins, advanced analytics and artificial intelligence will be key to productivity improvement...through 2022. The proliferation of digital products and subsystems to enable the IoT in downstream industries and generate revenue from smart products over their entire life cycle will be the most promising (and complex) driver for new IT spending growth through 2022."
The installation of a deeper, integrated refinery-wide information system that includes the processing operation history of each individual refinery unit will help to indicate or forecast operational upsets on these devices, enabling preventative measures to be undertaken prior to any upset. This deeper, integrated refinery-wide information system can include numerical computational methods along with more-recent computational neuro-science and chaos theory. A refiner looking to implement a deeper, integrated refinery-wide information system should also contact catalyst vendors and technology licensers to assist in optimizing operational parameter set-up to improve the results of the system, and help determine catalyst lifecycles.
Additionally, the plant revamps and upgrades section features the latest trends and technology offerings, including:
- A look at ongoing refinery revamps around the world aimed at boosting the quality of refined product output and/or processing different types of crudes (e.g., heavy crudes, light tight oil);
- Proper planning for a refinery turnaround;
- Improving turnaround health, safety, and environmental performance;
- A novel approach to revamps to lower turnaround time and costs;
- Revamping to improve refinery energy efficiency;
- Revamping a variety of refinery equipment (e.g., centrifugal compressors, heat exchangers, main fractionator, towers);
- Revamping of the crude preheat train to boost capacity of the crude unit;
- Adding an atmospheric preflash unit before the CDU as a means to absolve some of the reliability issues present in the preheat train and CDU when processing light tight oil;
- Adding a condensate splitter before the CDU for debottlenecking the crude unit when increasing light tight oil processing; and
- Applying Internet of Things (IoT) technologies (e.g., artificial intelligence, augmented reality, drones/robots, machine learning) to improve revamp performance.